The "Empower" Phase in the Thrive Cycle
May 15, 2024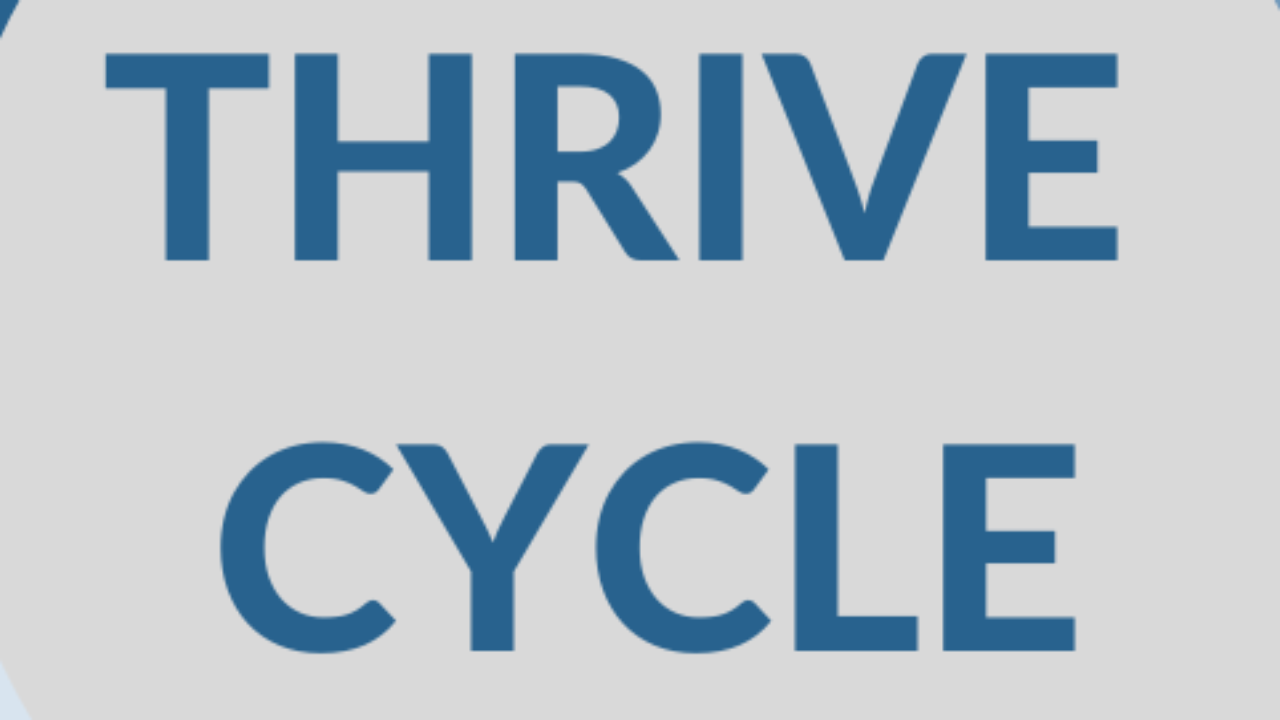
Celebrating Success and Fostering Continuous Improvement, Part 6
In the final stage of the Thrive Cycle, "Empower," small businesses are encouraged to solidify and sustain the improvements made throughout the earlier phases. This step emphasizes continuous improvement, celebrating achievements, and setting the stage for ongoing growth. By reflecting on successes and analyzing processes, businesses can create a culture of continuous improvement and readiness for future challenges. Integrating the concepts and tools from the "Control" stage of Lean Six Sigma enhances this phase, ensuring that gains are maintained and further opportunities for improvement are identified.
Understanding the "Empower" Phase
The "Empower" phase focuses on two key aspects:
1. Celebrating Success: Recognizing and celebrating the positive changes and successes achieved in the business and among the team members. This acknowledgment helps boost morale and reinforces the importance of everyone's contributions.
2. Continuous Improvement: Maintaining the improvements and creating a culture that encourages ongoing evaluation and optimization. This involves analyzing processes, identifying potential areas for further enhancement, and ensuring that changes are sustainable.
Implementing the "Empower" Phase in Small Businesses
1. Celebrate Successes:
o Recognition and Rewards: Publicly acknowledge the hard work and achievements of your team. This can be done through team meetings, awards, or other forms of recognition. Celebrating success motivates employees and fosters a positive work environment.
o Reflect on Achievements: Take the time to reflect on the improvements made and the journey taken to achieve them. Highlight the key milestones and the positive impact these changes have had on the business.
o Share Success Stories: Communicate the success stories within your business to inspire and motivate your team. Sharing these stories reinforces the benefits of continuous improvement and sets a positive example.
2. Continuous Improvement:
o Standardize Processes: Develop and implement standard operating procedures (SOPs) for the improved processes to ensure consistency and efficiency. Standardization helps maintain quality and prevents regression to old habits.
o Monitor Key Performance Indicators (KPIs): Continuously monitor KPIs to track the performance of implemented changes. Regularly reviewing these metrics helps in identifying deviations and areas that need further improvement.
o Feedback Loop: Establish a feedback loop where employees can share their observations and suggestions for further improvements. Encouraging feedback helps in identifying potential issues and opportunities for optimization.
3. Plan for Future Improvements:
o Root Cause Analysis: Continue to use root cause analysis to identify any underlying issues that may arise. This proactive approach helps in addressing new problems effectively.
o Identify New Opportunities: Look for new opportunities for improvement by analyzing market trends, customer feedback, and internal data. Staying proactive helps in anticipating challenges and capitalizing on new opportunities.
o Set New Goals: Based on the analysis and feedback, set new goals for the next cycle of improvements. This ensures that the business remains dynamic and adaptable to changing conditions.
Integrating Lean Six Sigma Concepts
The "Control" stage of Lean Six Sigma is integral to the "Empower" phase. It focuses on maintaining the gains achieved during the improvement process and ensuring long-term success. Here's how to integrate these concepts:
• Control Plans: Develop control plans that outline how to monitor and maintain the improved processes. Control plans should include detailed instructions on monitoring KPIs, handling deviations, and corrective actions.
• Statistical Process Control (SPC): Use SPC tools, such as control charts, to monitor process stability. Control charts help in identifying variations in the process and ensuring that they stay within acceptable limits.
• Visual Management: Implement visual management techniques to make key information readily accessible. This includes dashboards, scorecards, and other visual aids that display real-time performance data.
• Poka-Yoke (Error Proofing): Continue to use poka-yoke techniques to prevent errors and ensure consistent quality. Error-proofing mechanisms help in minimizing defects and maintaining high standards.
• Documentation and Training: Document all changes and improvements, and provide training to ensure that all employees are familiar with the new processes. Ongoing training helps in maintaining the improvements and fostering a culture of excellence.
By integrating Lean Six Sigma concepts into the "Empower" phase, businesses can create a robust framework for sustaining and building on their successes. This structured approach ensures that the improvements are maintained and that the organization is equipped to handle future challenges.
Creating a Strong and Positive Impact
1. Sustained Improvements:
The use of control plans and standardization ensures that the improvements made are sustained over the long term. This prevents regression and maintains the quality of processes.
2. Enhanced Team Morale:
Celebrating successes and recognizing team efforts boost morale and create a positive work environment. A motivated team is more likely to contribute to continuous improvement initiatives.
3. Proactive Problem Solving:
Regular monitoring and feedback loops enable businesses to identify and address issues proactively. This minimizes disruptions and ensures smooth operations.
4. Ongoing Growth and Adaptability:
By continuously seeking new opportunities for improvement, businesses can stay competitive and adaptable in a changing market. This proactive approach drives ongoing growth and success.
Overcoming Business and Market Challenges
1. Maintaining Quality and Consistency:
The "Control" stage ensures that quality and consistency are maintained, even as the business evolves. This is crucial for building and maintaining customer trust.
2. Adapting to Change:
Continuous improvement and monitoring enable businesses to quickly adapt to market changes. This agility is essential for staying ahead of competitors and meeting customer demands.
3. Minimizing Risks:
Proactive monitoring and error-proofing help in minimizing risks and preventing costly mistakes. This ensures smooth operations and protects the business from potential losses.
4. Fostering Innovation:
A culture of continuous improvement encourages innovation and creativity. This leads to the development of new products, services, and processes that can drive growth and differentiation.
The "Empower" phase in the Thrive Cycle is a critical component for any small business aiming for long-term success. By celebrating successes, maintaining improvements, and fostering a culture of continuous improvement, businesses can sustain their gains and prepare for future challenges. Integrating Lean Six Sigma concepts further enhances this process, providing a structured and data-driven approach to maintaining and building on successes.
At Thrive Business Consulting, we are committed to helping small businesses thrive by providing practical and effective solutions. Embrace the "Empower" phase today and take a significant step towards a more prosperous future for your business. For more insights and guidance, visit Thrive Business Consulting at https://www.helpyourbusinessthrive.com and let us help you turn your business hopes and dreams into achievements.